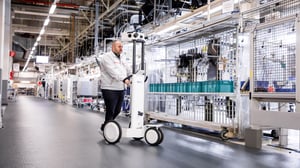
Never standing still, Audi steers towards virtualization
Audi site Neckarsulm, Germany, relies on NavVis reality capture solutions for their digital transformation.
Key takeaways
- Audi employs nearly 60,000 at their production sites in Ingolstadt and Neckarsulm, Germany.
- 250,000 square meters have been scanned at Neckarsulm in 34 working days; roughly 1,000 square meters per hour.
- All production halls at the Neckarsulm site will be scanned digitally, and then the neighboring site at Ingolstadt.
- Now that factory sites are virtually accessible, there's a reduced need for stakeholders to travel and visit the site in person.
- 3D scans are also used as the basis for artificial intelligence, machine learning, and virtual tours.
Forward through technology
Since 1899, the Audi brand is synonymous with performance vehicles of premium build quality and innovative design. The company is active in more than 100 markets worldwide, delivering around 1.8 million new Audi brand cars to customers during 2019. Audi’s longevity and success are simply explained by their legendary philosophy of Vorsprung durch Technik – a recent example of which is the digitization of production halls and buildings at their site in Neckarsulm.
A new vision for production planning
Audi currently employs almost 90,000 people worldwide, of which about 60,000 are employed at the German sites in Ingolstadt and Neckarsulm. “Virtual planning has of course been a topic with us for years,” says Bernd Widdmann, who heads the planning processes in the assembly department at the Ingolstadt and Neckarsulm locations.
Widdmann explains that in the beginning, the field was mainly concerned with the body shop, where large robots are used to assemble just a few parts. Today, however, this virtual planning is also being considered for final assembly, where multiple vehicle variants are produced by the machines side-by-side with employees. Processes can now be completely mapped, optimized, and simulated on the computer.
Where reality capture enters the equation is the ability to create a virtual model of the production site, which can be used as a reliable basis for production planning without the need to be physically at the site. The task of exploring this exciting possibility fell to project manager André Bongartz and his team. Working with NavVis since 2017, they figured out a way to integrate the point cloud data generated by NavVis mobile mapping systems with the existing planning systems in operation at Neckarsulm.
Scanning at 1,000 sqm an hour
"I probably know the Audi A6 assembly better than most A6 fitters now," says Alperen Öztürk. He used to work on the Audi A8 assembly line before he took over the operation of the NavVis M6 indoor mobile mapping system, gliding through the massive production halls.
Total area scanned to date is 250,000 square meters in 250 hours, or 34 working days. That roughly equates to 1,000 square meters per hour.
Öztürk steers the mobile mapper through each room at walking pace. The laser scanners above his head capture the surrounding area as he moves, and the initial contours of scan coverage are immediately visible on the display. In a very short time, an accurate digital image of the as-is conditions of existing buildings is created.
“Even while in home office, our factory planners are able to take measurements in production halls without being there or even picking up a ruler. These measurements are then used to create highly accurate plans of the facilities remotely.”
André BongartzPlanning Processes Methods/Standards
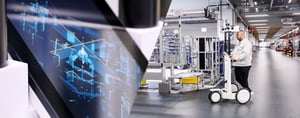
Machine learning and point clouds
After the data has been processed and made available from NavVis IndoorViewer, stakeholders can navigate through the virtual production halls using any standard web browser on a computer, tablet or smartphone. Users can look around and zoom in on production lines and machinery. Key details are visible and highlighted as points of interest.
Another benefit of the mobile mapping system, meanwhile, is the point cloud it has generated that records every machine and system. With the aid of machine learning, the point clouds are then incorporated into digital factory CAD models so that the entire hall, including all machines, systems and shelves, can be accessed and monitored virtually.
This has saved employees at Audi a great deal of time and cost – and realizes the goal of production planning that’s site independent. “Our digital planning system offers enormous advantages, especially now during the Coronavirus pandemic,” explains Bongartz.
"Even while in home office, our factory planners are able to take measurements in production halls without being there or even picking up a ruler. These measurements are then used to create highly accurate plans of the facilities remotely."
Future applications
For next steps, the plan is for all production halls at the Neckarsulm site to be scanned digitally, and then the neighboring site at Ingolstadt. Business trips to other factories around the world would become unnecessary if the factory buildings there also become virtually accessible.
Another possible application of the data generated by NavVis M6 are virtual factory tours. In the foreseeable future, visitors picking up their new cars may be able to move through the assembly line wearing 3D glasses and gain insights into areas that were previously closed to the public.
Data protection is still considered for these tours, as André Bongartz explains: “Even when production is at a standstill, there is always someone on the move in these halls.” So that no persons should be recognizable in the panoramic images, all faces are automatically blurred.
Images and video © 2021 AUDI AG. All rights reserved.
“Even when production is at a standstill, there is always someone on the move in these halls.”
André BongartzPlanning Processes Methods/Standards