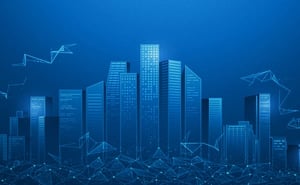
The definitive guide to scan-to-BIM
The term scan-to-BIM refers to a workflow that uses 3D scanning to document an existing asset and turn it into a Building Information Model (BIM). This process aligns older buildings with contemporary construction documents and planning methodologies, leveraging the advancements in BIM tools available on the market.
For more detail, let’s break it down term by term:
- Scan: 3D scanning technologies, e.g. mobile or terrestrial lidar. These tools are used because they capture an accurate, comprehensive, and detailed point cloud data set for the real-world building, which is foundational for scan-to-BIM projects. This data is essential for creating a precise model that integrates seamlessly with BIM tools.
- BIM: Building information modeling, a powerful AEC collaboration methodology. In a scan-to-BIM workflow, the final deliverable is a BIM-compliant 3D model, enhancing the effectiveness of construction documents and construction drawings throughout the project lifecycle.
Why should you care about scan-to-BIM?
Scan-to-BIM is an increasingly valuable (and lucrative) service for scanning providers to offer.
That’s because BIM is more than a passing trend for your AEC customers. The scan-to-BIM process is extremely effective in creating accurate BIM models, and these BIM tools can therefore enhance project collaboration and efficiency. BIM model-checking software allows for different disciplines of models to work together which can help identify clashes, or check specific constraints within the BIM model. This is another reason why scan-to-BIM is increasing in popularity. Many government bodies have even begun to mandate BIM, so its use in AEC will only continue to increase as time goes on.
The catch is that an AEC company needs detailed 3D models of a building to create good BIM models. For new projects, this is easy enough, since 3D data is generated by designers and planners during the early stage of the project.
However, for projects that aim to update existing buildings, getting 3D data for the asset isn’t quite so simple. That’s because a great majority of the buildings in the world were constructed before CAD modeling and other digital methods became popular. If the building comes with as-built documents or floor plans, they are often limited to 2D — or wrong. The most likely outcome is that the documentation just doesn’t exist.
Reality capture data not only helps overcome these challenges but also integrates seamlessly into BIM tools to be able to create accurate BIM models. This facilitates better planning, design, and management of construction projects. The adoption of scan-to-BIM practices allows for a more streamlined workflow by minimizing unforeseen issues and enhancing the overall project workflow, achieving better financial results.
BIM 101
Understanding the basics is important for anyone involved in a BIM construction project as it lays the foundation for implementing BIM tools and utilizing BIM model-checking software effectively. Generating detailed construction drawings are pivotal for the success of any construction project.
By making sure things are done correctly, AEC professionals can ensure their projects are built with the highest accuracy and efficiency, from initial scan-to-BIM processes through to project completion.
What is BIM?
Building Information Modeling (BIM) is a transformative process, utilizing digital representations of physical and functional characteristics of places. This methodology is backed up by the creation of detailed construction documents and construction drawings, facilitated by advanced BIM tools and scanners.
There is a standard, accepted definition of BIM. According to the National BIM Standard Project Committee in the USA:
“Building Information Modeling (BIM) is a digital representation of physical and functional characteristics of a facility. A BIM is a shared knowledge resource for information about a facility forming a reliable basis for decisions during its life-cycle; defined as existing from earliest conception to demolition.”
What is a BIM model?
As we discussed earlier, a BIM model is a 3D model optimized for use in the building information modeling methodology that make up an important part of construction documents used within BIM construction. This model serves as a digital twin of the physical building, incorporating construction drawings and plans that are vital for the planning, design, construction, and operation of buildings.
It includes spatial data, such as geometric design models or real-world 3D data captured by lidar or photogrammetry. The BIM model takes this a step further by connecting this spatial information to a database containing important functional and attribute data about the building. That might include materials used, size of rooms and spaces, or a breakdown of the interrelated parts of the HVAC system.
By utilizing BIM tools and BIM model-checking software, the BIM model facilitates a more integrated and detailed approach to building design and documentation, streamlining the scan-to-BIM workflow and enhancing collaboration among all project stakeholders. It can even include scheduling information or data about sustainability.
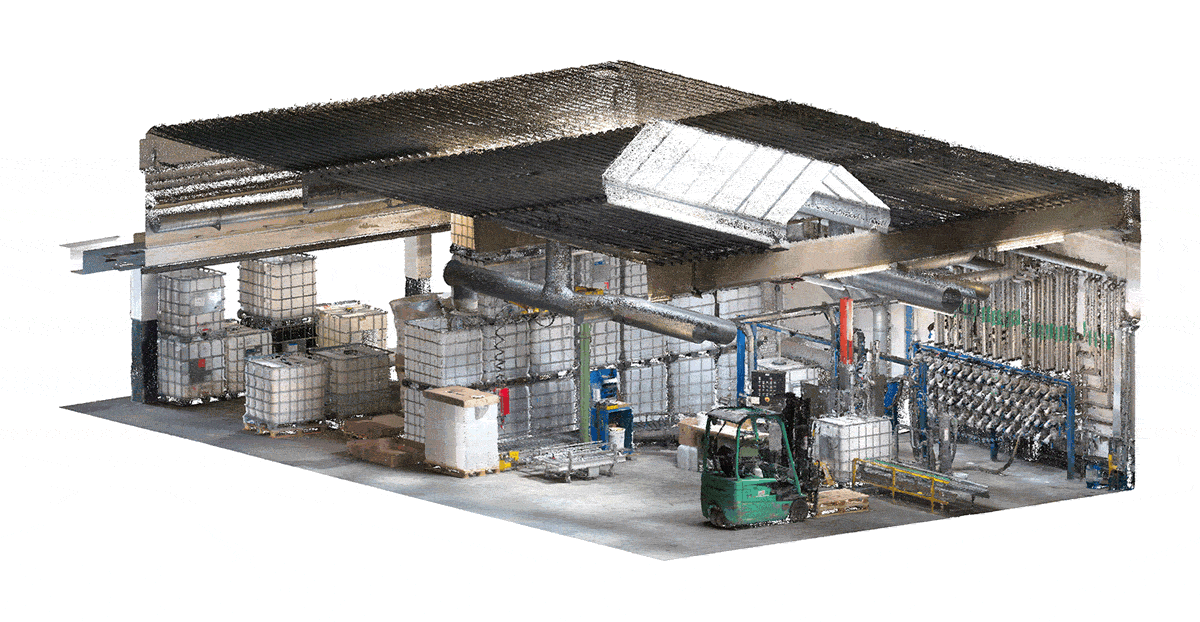
What is the value of BIM to your AEC customers?
BIM methodology lays the foundations for BIM models, and should be used in combination with with a common data environment (CDE). A CDE is a collaboration space where information from construction projects is stored and accessible to project participants. These methods allow for BIM to enhance the coordination and execution of construction documents and construction drawings.
This, in turn, helps teams to plan, design, construct, and manage a building much more effectively by keeping project stakeholders up to date, and enabling them to coordinate their work on an asset.
In short, BIM enables projects to keep work running smoothly, eliminate surprises, and improve their financial results.
BIM applications throughout the project and building lifecycle
BIM’s effects are complex and its benefits extend throughout the whole life of the building.
Here are three examples of how BIM can be used throughout the building lifecycle.
- Design and Planning
Good BIM enables trades to work together in a CDE and optimize building plans before construction begins.
For example, stakeholders can use it to perform a type of planning called BIM coordination, which orchestrates the work of MEP engineering, structural engineering, and architectural design teams during the design process. By combining the different design models into a “federated” BIM model, BIM coordination makes it easy to see clashes or scheduling problems as soon as they arise, like a run of pipe that exits through the floor rather than inside the wall. - Construction
A BIM model aids in the construction stage by making a wealth of information available (and easily understandable) to all stakeholders.
A properly generated BIM model will be accurate and include the most up-to-date design data from all trades, as well as important scheduling information. As a result, some projects will use it as a reference for prefabricating building elements. This model, refined through BIM model-checking software, contains the latest design data and scheduling details, facilitating the prefabrication of components. By using BIM tools, you can build elements offsite at tight tolerances. You can then move them to the asset for installation at precisely the right moment in the building sequence to prevent clashes. - Operations and Maintenance
Some estimates put 70% of the building’s total costs during this phase. A good, up-to-date and precise BIM model can go a long way toward reducing these costs.
The BIM model will include detailed, up-to-date information about a variety of building elements and systems. That means a maintenance worker or owner-operator could use it as a reference for information about the location and age of specific machines, how many parts are in an HVAC system, which kind of lightbulb a lamp uses, when repairs were last performed on a door, and a lot more.
→ BIM can help at various stages during the building lifecycle.
How to perform scan-to-BIM
Now that you understand what BIM is, and why it’s important to your AEC customers, let’s dig into how you can perform your own scan-to-BIM workflow to improve BIM construction.
Depending on what kinds of resources you read (and you’re probably going to read a lot about scan-to-BIM before you get out into the field) the workflow can be broken down in a number of ways. The scan-to-BIM workflow is multifaceted, typically encompassing stages like project planning, scanning, data processing, and modeling.
Stage 1: Project planning
Like any project, a scan-to-BIM project will require careful planning. Make time before work begins to talk with your client about their BIM requirments. Discuss questions like their intended applications for the BIM and their accuracy requirements. Compile all this information into a scope of work (SoW).
This will help prevent nasty surprises later in the project, and ensure that you and your client are on the same page.
Our guide to project planning can help you learn how to:
- Talk to your client about their needs
- Get important project details
- Use standards documents for absolute clarity
- Define a scope of work (SoW)
Stage 2: scan planning and field execution
Once you’ve locked down the project parameters with your client, you’ll need to plan the actual scanning work. No matter your level of experience, this is a good opportunity to make a solid plan for how best to approach the scan-to-BIM process and produce the best results for your client.
If you’re new to scan-to-BIM, be sure to think about this stage before you take on your first client. It will help you think about what kinds of scanners you’ll need for different kinds of projects.
Our guide to scan planning can help you learn how to:
- Pick the right scanner
- Develop a hybrid workflow
- Use survey control
- Make a scan plan
- Take notes
.jpg?width=1200&height=800&name=G11CustomerValidation-2257%20(1).jpg)
Stage 3: Data processing
After capturing the data, you’ll need to prepare it for the BIM modeling process. To do this, you’ll finalize the data in your processing software, clean up unwanted or erroneous data, register your scans together, and perform various checks to ensure that you’ve met coverage and quality requirements as agreed on in the scope of work.
If this is your first time processing data for a scan-to-BIM workflow, you’ll also want to ensure that your computing hardware can handle the huge data sets you’ll be working with.
Our processing guide can help you learn how to:
- Keep talking to your client
- Check your processing hardware
- Consider cloud processing
- Clean your data
- QA
- Register—and then QA again
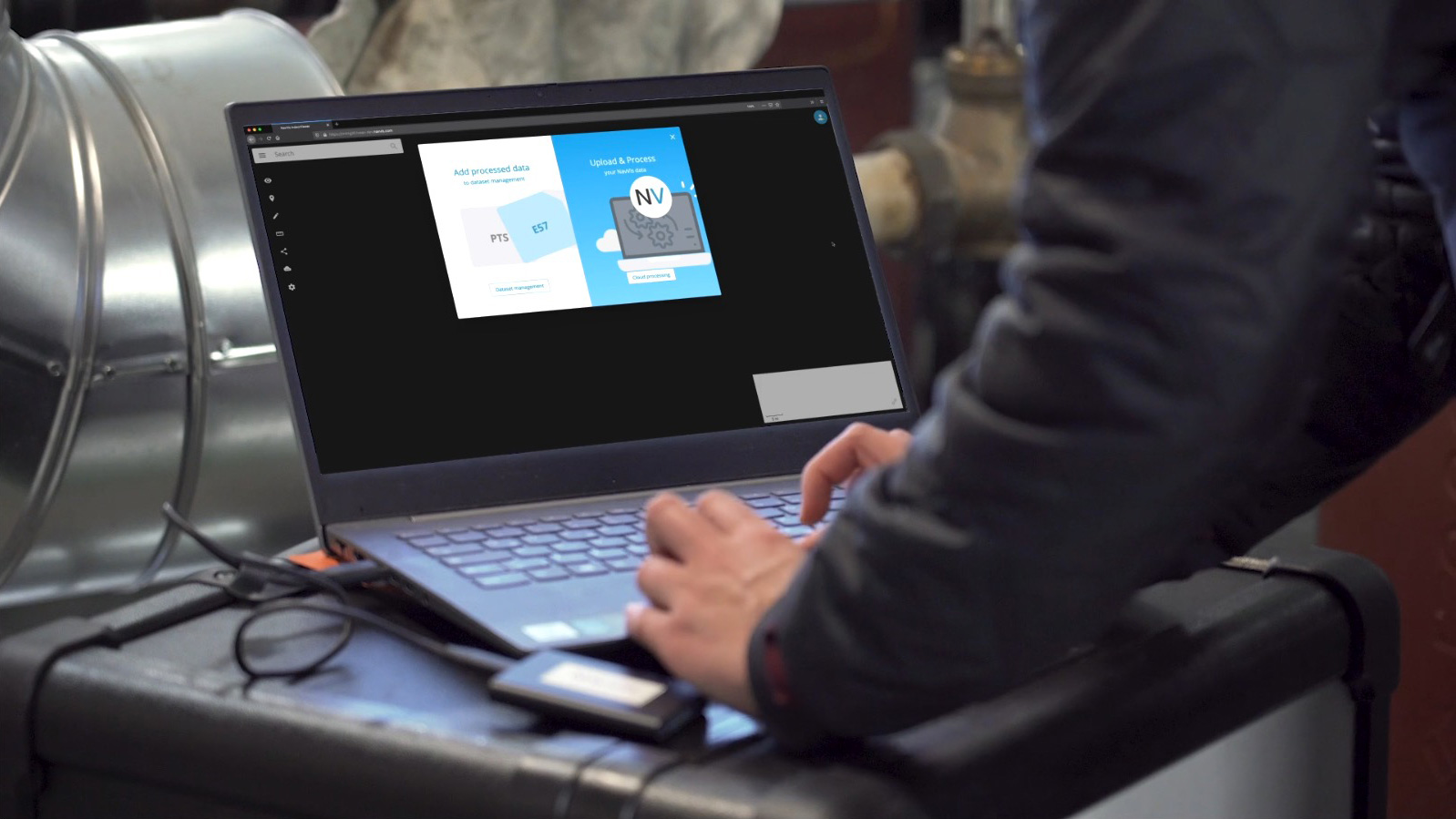
Stage 4: Modeling
Once the data is prepared and you have double- and triple-checked it to be sure that it meets requirements, you’ll turn that 3D data into a geometric BIM model.
If this is your first scan-to-BIM workflow, you’ll need to select your BIM modeling software from a range of options, determine your modeling personnel, and plan out your workflow to make the most of your employees’ time. At the end of this process, you’ll likely hand the work off to your client for their BIM work, so it’s your last chance to make sure everything is right.
Our modeling guide can help you learn how to do the following:
- Pick the right modeling tools
- Think about your modeler
- Time management is key
- Send your client a test model
Scan-to-BIM FAQ
You might still have some questions about BIM, or scan-to-BIM workflows. Here are answers to some of the most common ones.
What is the difference between BIM and VDC?
Building information modeling (BIM) and virtual design and construction (VDC) are both methodologies used by AEC professionals. The difference is focus: VDC is a method for using digital models, such as BIM models, to plan a construction project. The goal is to plan scheduling, finances, sequencing, and so on before any workers get into the field.
Note: VDC is typically used in the US, however, this terminology is not as popular in Europe. VDC is a common term to describe the process of using digital technologies (e.g. BIM, VR, AR, etc.)
BIM is a methodology for managing collaboration in the actual building and management process. VDC includes, but is not limited to, scan-to BIM methods within BIM construction projects.
What is the difference between a BIM model and a 3D CAD model?
Both types of models contain geometric information about a real-world structure. However, 3D CAD uses “dumb” lines to represent a building, meaning the lines are not grouped together into objects within the model, which can limit their functionality in BIM tools.
For example, you may look at a drawing of a window in a CAD model and know that you are looking at a window, but the CAD model thinks of that window as a set of unrelated lines.
BIM models, on the other hand, do group lines into objects. The BIM model will know that a window is a window. This is useful for linking geometric information to semantic information about the asset. This object-oriented approach is beneficial for integrating geometric and functional information, and creating a database of the building within construction documents and construction drawings.
What is the difference between a BIM model and a digital twin?
You can think of a BIM model as being a step on the way to a digital twin.
The evolution from a BIM model to a digital twin represents a leap in how buildings are represented and managed within BIM tools. While a BIM model provides a detailed digital representation crucial for creating construction documents and aiding the scan-to-BIM workflow, a digital twin enriches this model with real-time data from IoT sensors.
This live data feed can measure the movement of a crowd, temperature throughout the different spaces, gas levels, and anything else that can be captured by sensors.
In other words, it’s exactly what it sounds like: A digital “twin” of the real-world building as it exists right now, in the real world.
This extra data enables digital twins to look into the future through simulation and is a huge advantage of BIM construction. Many owner-operators will process a digital twin’s real-time data with machine learning or other AI tech and use it to test out possible changes to the asset. That could tell you, for instance, what might happen to the pedestrian paths if an extra outdoor staircase were added. Or it could tell how much faster your assembly line might operate if you moved that shelf of parts closer to a specific worker.
What is 4D BIM? 5D BIM?
BIM “dimensions” refer to the types of information reflected in the BIM construction model. Here is a quick overview:
- 3D BIM is the classic BIM construction model. It includes spatial (i.e., three-dimensional) information and a database of functional information.
- 4D BIM construction models add scheduling information, corresponding to the dimension of time. This enables projects to sequence their construction to avoid clashes.
- 5D BIM construction models add cost information. This is a loose definition of a “dimension,” but it enables projects to do more precise financial planning by seeing what costs will be at different stages of the construction sequence.
- 6D, 7D, 8D… are non-standard BIM dimensions. Some projects or agencies will use them to refer to information like sustainability, but its best to stay away from these designations and discuss the necessary data directly with your client instead.
→ The NBS website has more information about the different levels of BIM.
What are the BIM levels?
A BIM level refers to the maturity level of the BIM used by a specific project. It indicates the extent of collaboration between stakeholders, and the level of digitization of the project.
- Level 0 – Essentially the absence of BIM, this means little to no collaboration and zero digitization. This means heavily reliant on traditional methods such as 2D CAD.
- Level 1 – Partial collaboration between different disciplines on the project. Projects use 2D and 3D CAD for creating construction documents and drawings, and information is shared in a common data environment (CDE).
- Level 2 – Stakeholders are managing projects across disciplines with the use of the intelligent BIM models and combine their data in a CDE. The projects most likely uses 4D or 5D BIM model.
- Level 3 – Improves on level 2 by bringing full integration. Intelligent data sets are combined in a single, federated model which operates as a single source of truth. This model uses collaborative and digitized construction documents and drawings, supported by BIM model-checking software and optimized through scan-to-BIM processes.
These levels constitute the strategic roadmap for the construction industry, with the UK mandating level 2 for all projects in 2016.

Try it yourself
Take the next step in the mobile mapping revolution
The speed and scalability of mobile mapping devices are the best they've ever been, bringing survey-grade accuracy to the most challenging projects. Get hands on with NavVis VLX and see for yourself what's possible. This tool embodies the latest in mobile mapping and simultaneous localization and mapping, offering unparalleled accuracy and efficiency for even the most challenging projects.