
What is topographic surveying?
Everything you need to know about topographic surveying with SLAM scanners
Introduction
You’ve heard big claims about simultaneous localization and mapping (SLAM) scanners: The technology can help you complete surveys faster, capture richer context for the site, and improve your deliverables. It can even keep you safer in the field.
But you’re skeptical. As a professional whose reputation depends on choosing the right technology, you need to know more before you commit. How does SLAM scanning actually work? How do you use it for topographic survey? Is the workflow complex? Is it accurate enough? It looks like a black-box technology, so how can you trust the results?
This guide will answer all these questions and more. We’ll begin with the basics of topographic survey, then the pros and cons of today’s most common survey tools. After that, we’ll explain what SLAM scanning is, how it works, how to use it, and what it can do for you.
Let’s get started.
Watch NavVis technology in action behind the scenes of real projects
What is a topographic survey?
A topographic survey, sometimes called a topo or detail survey, maps the boundaries and features of a parcel of land. It produces an accurate map of current topographic conditions, usually as preparation for engineering or construction projects.
Depending on the project, the final survey deliverable might include contour lines, boundary lines, natural features, buildings and structures, curbs, road furniture like signage and lamp posts, utilities, or other features.
Workflow: Traditional topographic survey
Tools
Robotic total station, prism, and GPS systems. A robotic total station measures distances and angles with great precision, while a prism is designed to reflect the beam of a total station; GPS equipment provides accurate location on the Earth's surface and helps you set up the appropriate coordinate system for the survey, while it is only sometimes used for the actual capture of points on-site in urban areas.
- Lay out control points and survey them with your GPS equipment
- Transfer these control point coordinates to the total station as the basis for all other points
- Set up the total station where it has a clear line of sight to the area being surveyed
- Walk to the first feature
- Capture survey points for the feature using prism and GPS equipment
- Repeat until the survey is complete, moving the prism and GPS equipment as needed
- Return to the office
- Process and analyze the data
- Draft survey deliverables (maps, reports, models, etc.)
Common deliverables
- Digital elevation model (DEM): A 3D representation of the Earth’s bare surface, excluding natural features. Indicates elevation values at regular intervals.
- Digital terrain model (DTM): A 3D model that augments the DEM with natural features such as rivers, vegetation, etc.
- 3D building models: A geo-located model that indicates the position, layout, and dimensions of any structures on site.
- Computer-aided drafting (CAD) map: A 2D map that uses points and line drawings to indicate all necessary details and features.
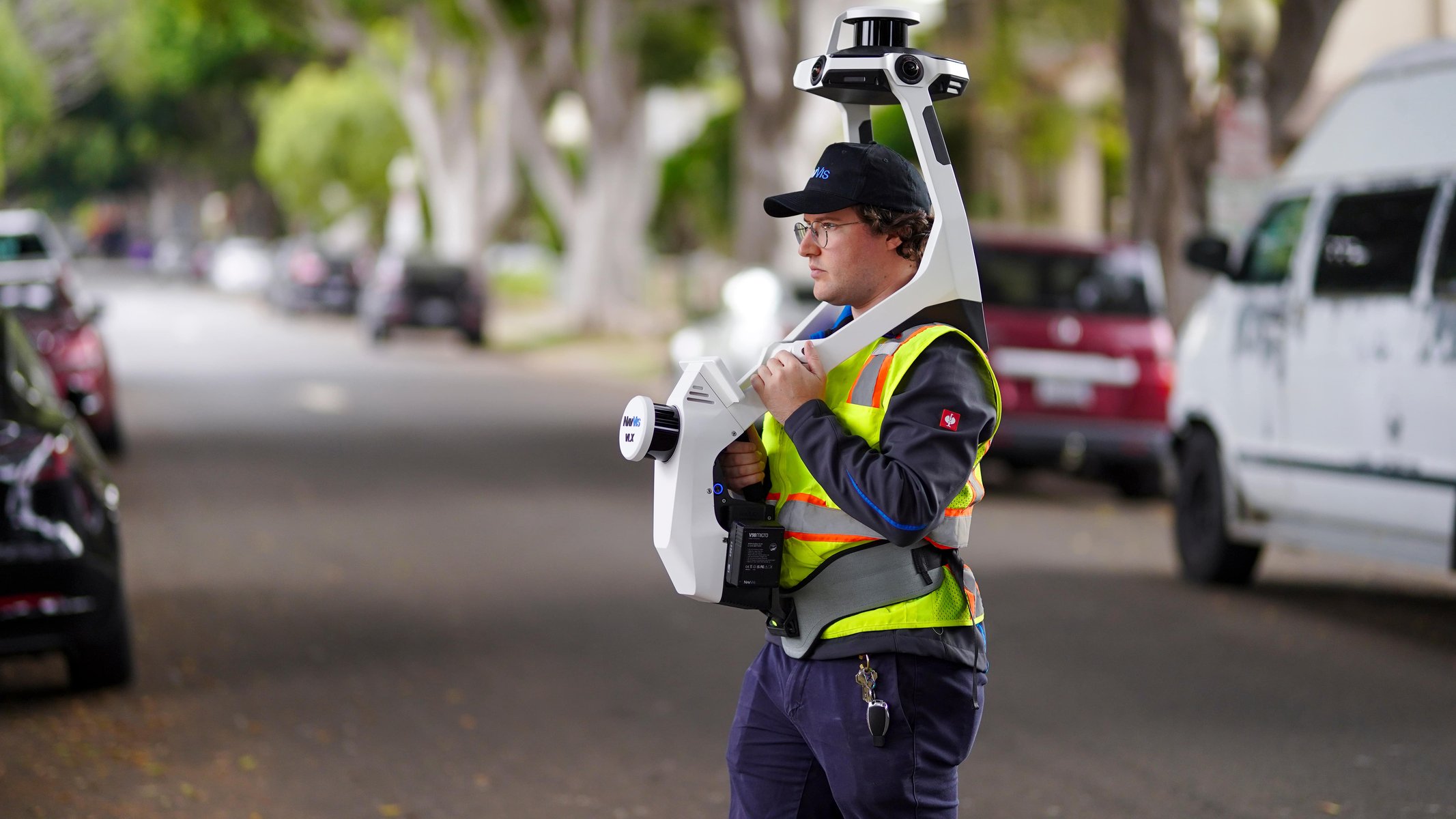
Workflow: Virtual survey with a terrestrial laser scanner (TLS)
Tools
Scanning total station or terrestrial laser scanner. These use lidar (light detection and ranging) sensors to capture a large number of site measurements, creating a dense and accurate 3D dataset known as a point cloud. Total stations or GPS systems are normally used to set up the control network to which the point cloud of the terrestrial laser scanner will tie in.
- Set up the scanner to ensure maximum coverage with minimal obstructions
- Capture a point cloud
- Move the scanner to the next location ensuring overlap with previous scans for full coverage
- Repeat these steps until you have covered the whole site
- Return to the office
- Register the individual point clouds together using specialized point cloud software
- Perform survey measurements using virtual survey software
- Draft survey deliverables
Common deliverables
- Digital elevation model (DEM): A 3D representation of the Earth’s bare surface, excluding natural features. Indicates elevation values at regular intervals.
- Digital terrain model (DTM): A 3D model that augments the DEM with natural features such as rivers, vegetation, etc.
- 3D building models: A geo-located model that indicates the position, layout, and dimensions of any structures on site.
- Computer-aided drafting (CAD) map: A 2D map that uses points and line drawings to indicate all necessary details and features.
Check NavVis VLX 3 in action!
Denn Engineers, a top US surveying firm, tested NavVis technology against traditional survey methods in a complex urban area.
— Point cloud data in .e57
— CAD file in .dwg and .dxf
— Plot in .pdf
— A topographic survey workflow comparison in .pdf
Pain points
These workflows provide reliable ways to survey a site from boundary to boundary. But both present significant challenges.
Here are the most common pain points for traditional surveys.
- Deliberate and time-consuming
Surveying with a total station is a meticulous process that requires capturing a lot of measurements to accurately define features. Think of a simple feature like a straight curb: You’ll need to capture a survey point every 15-20 meters to define the line. If the curb includes curves, you’ll need to capture an extra three points. And you will need to capture even more points for more complex features. On a large site with numerous complex features, the number of survey points grows quickly—as does the project duration. And it is not about the number of measurements, but about walking between them. To capture a road, for example, you would walk the length of the curb, trace this feature, walk back down the curb to record the channel line, walk up to the center of the road to record the center line, and finally repeat all this for the other side of the road. So, the length of a simple stretch of road ends up being covered multiple times, taking considerable time and energy. - Perceived slowness with a static scanner
Tripod-mounted laser scanners are much faster than traditional total stations, but they can still feel slow and deliberate. Adding the time to set up the scanner, make your capture, and move to the next station, it will take you longer than necessary to get a single point cloud. When a survey requires even a dozen setups, that can mean a long time in the field. - Traditional surveys are not comprehensive
Best practice for total station survey says you should only survey features defined in the project scope. This approach, while efficient in terms of project focus, can become inefficient if project requirements change or expand. So the problem comes when a stakeholder contacts you later to ask for survey details on a feature outside the scope, like a boundary or curb line. This requires a return to the site and a second survey, at extra time and expense. - Gaps in data
A laser scanner can only capture features within its line of sight. If you don’t plan carefully, accounting for every occlusion and adding extra scans to ensure good coverage, you may end up with blank spots in your scan data. And the feature you’re trying to survey could be lost in one of those blank spots. - Safety concerns
The need to physically place prisms or GPS equipment - or detail poles - near survey points can pose significant safety risks. Surveying a road line, for example, means standing in the center of a busy road. It is easy to imagine how this is a serious concern in traditional survey workflows. - Lack of photographic documentation
Photographs add rich, valuable context to any survey. Unfortunately, most classic equipment does not automatically capture all the images you want. That means it’s up to you, the surveyor, to manually capture photos. While you’re already busy completing a complex survey. The result is that photographic coverage often takes a back seat.

Advancements in survey tech: SLAM scanning
Simultaneous localization and mapping (SLAM) scanners promise to change how we perform topographic survey.
A SLAM scanner is much like a terrestrial scanner in that it captures 3D data fit for use in a virtual survey workflow. However, SLAM scanners are different in one very important way: They exploit sophisticated sensors and algorithms to make huge improvements to your 3D capture workflow.
These devices enable you to capture 3D data at walking speed. They produce fully colored, photorealistic point clouds; automate the registration process; and even reduce your travel expenses. And that’s not all.
But before we dive into the benefits, let’s start at the beginning and answer some of your basic questions about SLAM.
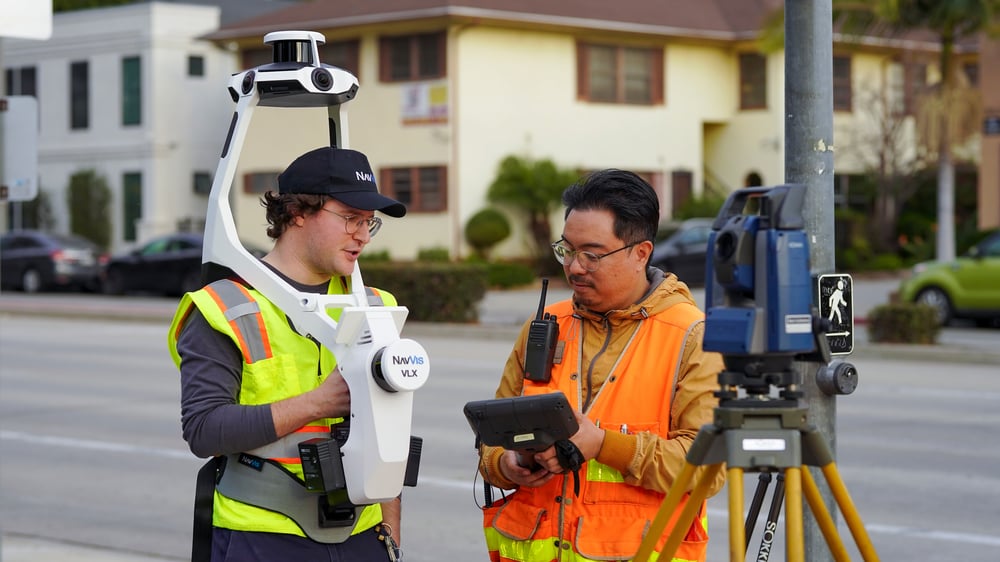
Intro to SLAM
SLAM is not a specific hardware or software but a broad term for a technological process. It was developed in the ‘80s to help robots navigate autonomously through new environments without a map. Today, SLAM is used in various applications, from autonomous vehicles to smartphone augmented reality apps. It is also a crucial element in the latest generation of laser scanners.
There are many approaches to SLAM, but the basic idea is similar across all implementations. To demonstrate how it works, here’s a high-level explanation of the SLAM process in 3D scanning:
- You turn on the SLAM scanner
- It captures your surroundings using lidar, cameras, and other sensors
- The SLAM algorithm processes this data to “identify” features around you
- It uses these features to build a rough 3D map
- And estimates its own location on that map
- When you move the device, it collects new data from its sensors
- The SLAM algorithm uses this data to improve its 3D map
- Which helps it improve its location estimate
- And so on
Repeating these steps thousands of times per second, a top-grade SLAM scanner like NavVis VLX 3 tracks its own path as you carry it. It also builds a crisp 3D map of the site at a very high level of accuracy.
Check out our comprehensive educational guide here for a much more in-depth exploration of SLAM →
SLAM is like total station survey
You may read that explanation and still think that SLAM feels like a black-box technology. If so, it may help to learn that a good SLAM scanner relies on many of the same principles as a good total-station survey.
Foresight and backsight readings
In traditional total station surveys, foresight and backsight readings are critical for accuracy. Backsight readings involve pointing the total station towards a reference point with a known elevation, while foresight readings are taken towards the new point to be measured. These readings help establish the position and elevation of the total station and the point being surveyed.
SLAM scanners also reference previously established points to determine their position in three dimensions. While you might make these calculations every so often, a SLAM scanner does it continuously, improving the accuracy and precision of its measurements.
Traverse closures
When you’re working with total station, you’ll sometimes complete the job by surveying the starting point again. This is called a closed traverse, and it allows you to check and correct for any discrepancies or errors in the measurements. You can do the equivalent with a SLAM scanner by performing a loop closure.
Simply return to a previously captured area. The system will automatically use this known location as a reference point, take more readings, and correct errors that may have accumulated throughout the scan.
Control network
You begin a survey by setting a control network, which involves establishing survey points and benchmarks. This grid becomes a reference for all other survey readings you take throughout the survey.
Some advanced SLAM scanners, like NavVis VLX 3, can also use a control network as a reference. When you process the data in the cloud, sophisticated algorithms will use these control points—in addition to the readings we mentioned above—to tighten up the accuracy of the final point cloud.

Workflow: SLAM scanning for topo or detail surveys
Though each SLAM scanner offers its own unique workflow, the general idea is the same. Here’s how to capture a topographic survey using NavVis VLX 3:
- Establish a survey control network across the site
- Walk the site with a NavVis VLX 3 to capture a 3D data set and HD panoramas
- Use the built-in touchscreen interface to monitor your scanning progress in real time and mark control points
- Align the belt hook of NavVis VLX 3 with control points to trigger their capture
- Save your data and upload it to NavVis IVION for cloud processing and optimization
- Produce any other desired survey deliverable using specialized software
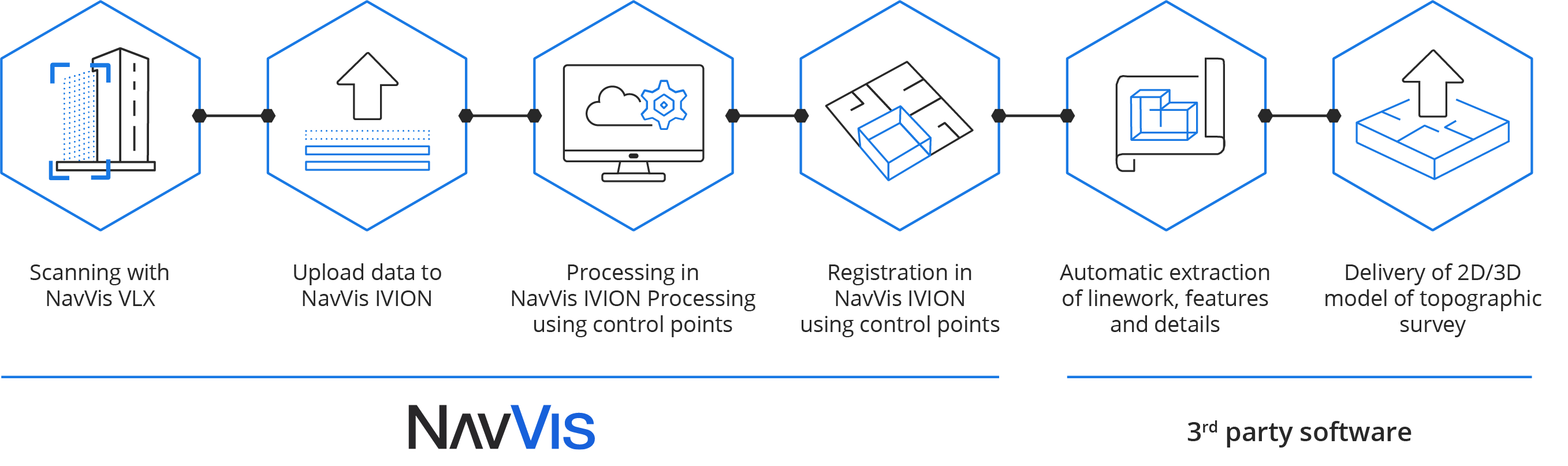
Featured news
.jpg?width=300&name=NavVis-VLX-3-Culver-Street-linework-517-webinar-advancing-topographic-surveys-events-page-04092024-wp-featured%20(1).jpg)
On-demand webinar Advancing Topographic Surveys:
The Role of Wearable Mobile Mapping
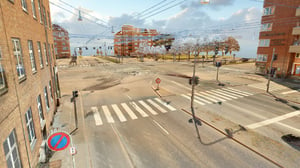
On-demand webinar Next-Gen Topographic Mapping: Exploring Wearable Mobile Technology

Sample data Environment: Urban road - Los Angeles, USA

E-book Beyond Boundaries: NavVis VLX in the field
Ten benefits of SLAM scanning in topo and detail survey (plus one)
SLAM scanning offers several huge benefits in topo and detail survey.
1. Accelerated capture
First, the big one: speed. Since SLAM scanners capture 3D data as you walk, they expedite capture workflows significantly. Consider a site that would take 11 hours to capture with a total station. Years of field testing and professional experience have shown you could complete the same capture in just 2 hours with a SLAM scanner.
Find out just how fast NavVis VLX 3 is compared to a terrestrial laser scanner →
2. Good accuracy
Surveyors were skeptical of early SLAM scanners because they produced point clouds with low accuracy. Today, the technology is fully mature.
A top-grade SLAM scanning system like NavVis VLX 3 can produce a point cloud of 5 mm accuracy or better, especially when you snap the data down to survey control. That data is more than accurate enough to discern elements like the front of curb and back of curb. Or to produce deliverables like DTMs, DEMs, or CAD maps.
3. No missing data
SLAM scanners like NavVis VLX 3 include a built-in touchscreen interface that offers live visual feedback on scanning progress. The screen makes it easy to spot a shadow in the data and fill it in by walking around an occlusion. The result is a comprehensive 3D data set with measurements for every feature on site.
4. Automatic registration
Most of the time, a total station - which generates one point cloud for each capture - will be set up on a survey nail, or its position will be established via resection; when this does not happen, before preparing deliverables, you'll need to register together all the point clouds generated. Unfortunately, the registration process for tripod-based scanners is often time-intensive.
SLAM scanning systems automate this registration process to save you time. NavVis VLX 3, for example, harnesses all the computational power of NavVis IVION to process, optimize, and geo-register point clouds with minimal human oversight.
5. Photo-realistic point clouds
A SLAM scanner like NavVis VLX 3 uses multiple 360° cameras to capture high-definition imagery as you walk. During the processing stage, the companion software, NavVis IVION, combines these photos with the point cloud to produce a photo-realistic 3D data set.
You can use these colorized point clouds to examine details around the site, just like looking at photographs (but better, because you can take measurements, too). You can zoom in on road lines, curbs, and structures for a close look and answer questions like, Is the road cracking? Is the pavement fresh? Does this bus shelter need replacement?
6. Automated CAD deliverables
If you want to speed up your survey workflow further, you can export your point cloud after processing and use 3rd party tools like TopoDOT, n4ce, and SCC-CAD to automatically extract linework, features, and details for producing high-quality CAD deliverables quickly.
7. Improved safety
A SLAM scanner like NavVis VLX 3 can capture measurements to an operational range of 50 meters. That means you can get data on road lines or other details without putting yourself in danger.
8. No traffic closures
By keeping you out of the road, SLAM scanning eliminates the need for traffic closures when performing a topo or detail survey of a roadway. The result is significant savings for your client.
9. Reduced travel time and expenses
A SLAM scanner produces a comprehensive, detailed, and accurate 3D data set that enables you to perform a virtual survey from the office. As a result, when a project stakeholder needs new survey data not defined in the original scope, you can simply open up the 3D data set in your software and perform another virtual survey—no travel required.
10. Versatility
SLAM scanning systems are robust enough for use in many environments, including office interiors, industrial facilities, construction sites, parking garages, utility buildings, bridges, and urban environments like intersections.
11. Efficient (and happy) crew
Another fundamental plus on site. Field teams can be difficult to staff, as skilled labor is scarce. Employing SLAM technology in topographic and detail surveys has the considerable advantage of keeping the field crew more efficient as well as provide the opportunity to take on more projects with your existing team. The quality of your jobs will improve, and with most of the work being moved from busy streets at the mercy of the weather to the office, your team will be happier.

The real-world economics of SLAM scanning
Let’s explore what these benefits mean for a surveying business. Here are a few real-world tests where NavVis’ customers compared NavVis VLX 3 against traditional survey methods.
Urban road capture
We are talking about a detail survey of a road junction — a site of approximately 5,000 sqm with few obstacles, a low amount of occlusions, consistent lighting, a long line of sight, and a large field of view.
Compared to traditional survey methods, NavVis VLX 3 offers:
- 2.5X faster acquisition
- 2.1X faster office work
- A 35% total reduction in labor time
A NavVis customer reduced the time spent on site by a remarkable 87.5%, with fewer traffic management outlays and lower overall costs.
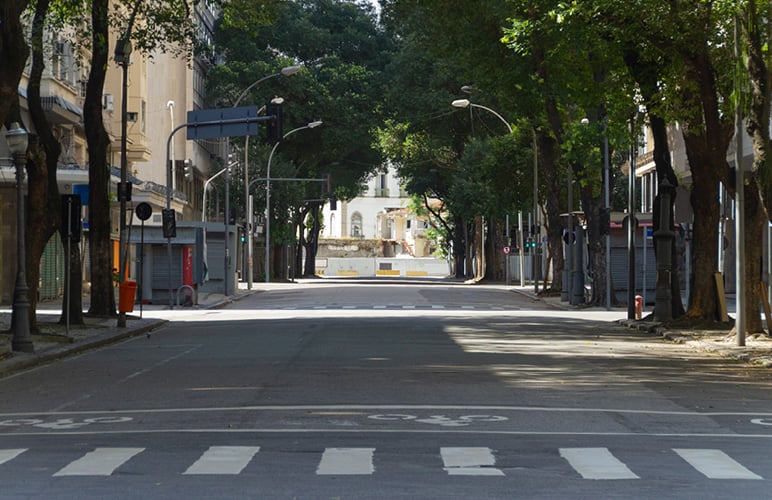
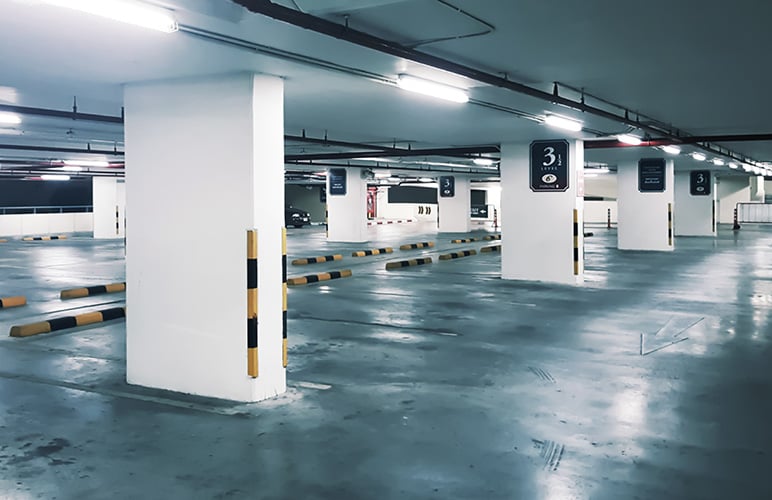
Parking garage survey
Here, we survey 45,000 sqm of empty parking lot with similar capture conditions.
Compared to traditional survey methods, NavVis VLX 3 offers:
- 2.5X faster data acquisition
- 4.2X faster office work
- A 57% total reduction in labor time
.jpg?width=300&name=NavVis-VLX-3-Culver-Street-linework-517-webinar-advancing-topographic-surveys-events-page-04092024-wp-featured%20(1).jpg)
Get the latest news as it happens
You'll get the latest updates, news, and industry insights – plus the occasional newsflash – direct from the team at NavVis.